“We are not given a dream unless we also have the power to make it happen.” –PMPA President Darlene Miller.
I was in the audience when she made that comment at a meeting of students considering their future careers.
That quote resurfaced over the weekend when my son, a CNC operator, sent me the following video “What Do Machinists Dream of?”
[youtube http://www.youtube.com/watch?v=88q3ZoYUKEg&w=560&h=315]
It made me smile, because our machinists can in fact make the high precision, high reliability components shown in the video needed for the sponsor’s “Dream Mission.”
What you dream is important, because it determines what you have the power to achieve. What do you dream of ?
If you dream of an interesting and well paying career, you might want to investigate precision machining.
And yes, we can make the stuff that you see in the video in our shops.
“Moon Mission, anyone?”
Poncari Sweat is a sports drink
Tag: Darlene Miller
It is easy for big city editors and academics to broadly dismiss the real issues that employers face as we try to find and hire skilled workers. There are systemic disincentives and cultural issues that are discouraging people from getting the skills that could lead to a great career in precision machining and advanced manufacturing.
PMPA President and Member Darlene Miller, President and CEO of Permac Industries in Burnsville, MN was mentioned in INC Magazine’s Latest Article on the Skills Gap.
The article shares the success of Darlene Miller’s efforts to jump start the creation of a training program for machinists in her area.
“Darlene Miller, CEO and owner of Permac Industries in Burnsville and a former member of the President’s Council on Jobs and Competitiveness, contacted the Manufacturing Institute to develop a fast-track program, Right Skills Now. Area companies worked closely with two community colleges to create a 24-week intensive course, including internship, that launched in October 2012.
So far, businesses are happy with the result; graduates “are scarfed up as soon as they finish,” Miller says. The program has spread to eight states; four groups of 18 to 20 people have finished in Minnesota, with a placement rate approaching 95 percent.”
But the INC Article glosses over some very critical issues in an attempt to poo-poo the fact that “there are issues finding people for specific jobs in specific industries;” and states that in the workforce as a whole there is no skills gap.
Issue: Schools are not preparing students for careers in advanced manufacturing. Check..
- Weak math skills in applicants,
- Inability to use ruler, let alone micrometers or more sophisticated gaging,
- Lack of shop classes in most school districts.
These are facts that we face with most applicants right out of school.
Issue: Unmotivated workforce. Check.
- Workforce participation rate has never been lower since they started keeping track of it.
- Why work when you can collect benefits?
- Our shop owners report that many applicants are just going through the motions since they still have many weeks of extended federal benefits.
- Also many applicants can’t pass a drug test. One PMPA member told me that they lost 2/3 of their new hires within a year for either drugs or failure to show up to work as scheduled.
This is reality. Generous unemployment benefits and their extension provide a disincentive to people to work.
Issue: Employers aren’t training. Hogwash.
- Our shops provide many forms of training to our new hires as well as our established employees.
- Many provide training in house through ToolingU.
- Many have arrangements with local schools to provide coursework on premises.
- Many have tuition Reimbursement Programs.
- Also, PMPA provides CEU recognition to member company employees who attend association provided training events.
It is easy for big city editors and academics to broadly dismiss the real issues that employers face as we try to find and hire skilled workers.Skilled workers to add value in our advanced manufacturing precision machining shops. But the facts that our shop owners face daily establish that there is a skills gap in our industry. Despite the best efforts of our company managements, trade association, and community colleges to make a difference, there are systemic disincentives and cultural issues that are discouraging people from getting the skills that could lead to a great career in precision machining and advanced manufacturing.
What are you doing to address the skills gap? How do you see the skills gap in your efforts to add talent?
Photo credits INC Magazine
“With aerospace function and safety criticality, we absolutely need to know the status and location of every piece that could be considered a part. We have definitely upped our performance in the accuracy, flow and knowledge of status of “what’s in the bin.””- Tammy Wilson.
Permac Industries recently announced that they were just awarded their AS9100 certification, on their first try. AS9100 Certification is required by many OEM’s in the Aerospace industry.
I asked a group of employees at Permac what were the unexpected challenges and what made their efforts work.
If you are a manager, you might want to jot a few of these down.
Challenges
- Weren’t able to foresee many of the additional requirements.
- Weren’t able to understand the impact of some of these requirements on our processes;
- Weren’t really expecting additional paperwork- Our previous experience with Quality System implementations were that they helped us lean out our paperwork;
- Really had to embrace the Authority of piece count and build processes based on count.
Enablers of Success
- We really did have the right people in place;
- Those people had both the responsibility and authority to make the system and process improvements demanded by the AS9100 standard;
- They had management support when the changes were difficult to implement
- They felt that management was confident in their ability to make the changes.
Members of the team told me that
- Having strong existing systems made their job easier- they didn’t have to reinvent anything.
- They did need to tighten up procedures;
- They did need to add some additional procedures;
- They have focused more on supplier and production control
Congratulations to the team at Permac for getting this done right first time.
Do you have a success story to share?
There is no reason that the vast majority of new manufacturing jobs have gone to men, but they have.

Why has womens’ representation in manufacturing dropped for two decades?
PMPA Vice President Darlene Miller testified before the Senate Joint Economic Committee last week on the topic of Women in Manufacturing.
As a shop owner, STEP Women in Manufacturing honoree, and member of the President’s Job Council, Darlene has some real world insight into the issue.
Here are her 4 Steps to Encourage Women in Manufacturing Careers
1) It is absolutely essential that businesses engage with local community colleges to assure relevant skills sets are being taught;
2) Equipment needs to be current, not old and outdated. We have high tech $400,000-$500,000 equipment per machine.
3) We really need really excellent math and problem solving skills; we need to tell the Schools what those are.
4) We need to get into middle schools to engage female students at a younger age to potential careers.
Watch the testimony:
[youtube http://www.youtube.com/watch?v=WN3JQkE3gng&w=420&h=315]
Read the report:
Women in Manufacturing PDF
Lack of skills were found to be behind the skills gap for production jobs according to a new report by Twin Cities Business Magazine.
“Only in production work did lack of training seem to be a barrier for job candidates, and in about half of those cases, the training they lacked was technical training at the high school level—the sort of program that has disappeared from many schools.”
PMPA’s Vice President, Darlene Miller states in the article “I don’t think it’s coincidental that when our [high school] dropout rate increased by 30 percent was when all of our technical classes in our high schools ended.” And that is when industry lost its pipeline of potential skilled workers.
Three ideas to get back on track from the article:
1) European Educational Model. “We need to get back in the European path,” Miller says. “They really show students at [middle school] age, what are your potential career paths. And manufacturing and the trades are viewed just as highly as any other career.”
2) Build career awareness in younger students. “It’s costly to wait until people reach college age or older before introducing them to technical careers and skills. Rather than playing catch-up, employers and educators want to start the process earlier, not only with STEM education that emphasizes science, technology, engineering, and math in K–12 schools, but through more direct work with kids.”
3) Overcome parental fears about “vocational track’ education. Despite the fact that 54% of the unemployed have bachelor’s degrees, most parents still equate a college education with job security. “Parents worry about schools “tracking” their children at a young age: pushing them to choose between the path to college and the path to technical school, and closing off the road not taken.”

The Twin Cities Business Article concludes with comments from Darlene Miller on the skills gap: “The economic security and upward mobility that have long been the perceived promise of a four-year college degree are less certain now, it’s “skills that pay the bills.”
“When we understand that 54 percent of our unemployed are college graduates, what does that tell us? It tells us that we’ve been training people for jobs that don’t exist,” she says. Just as some wonder whether the skills gap is real, Miller suggests that one of its sources—the notion that a bachelor’s degree is always the right choice—is a fiction.
“Is going into debt and spending six or more years to get a four-year college degree, and then not having any assurance of finding a job to cover that investment when you’re done, is that really real?”
Skills do pay the bills.
PMPA has a number of resources to help you explore a possible career in precision machining advanced manufacturing.
When I started in manufacturing, “The Gals” were in the office- not the shop.

The inaugural group of 122 STEP honorees recognized by the Manufacturing Institute on February 5th in Washington D.C. showed me that the times have changed and that there are many, many ways that women can and do meaningfully contribute to manufacturing at their companies as
- Plant and Production Managers,
- Operations,
- Engineers,
- Technologists,
- Process Control,
- Regulatory Affairs,
- Certified Welders,
- CNC Machine Operators,
- Weld Process Specialists,
- Quality Control,
- Health,
- Environment,
- Process Safety,
- Chief Financial Officer,
- Designers and Design Engineers,
- Compliance Officers,
- Chief Scientists,
- Safety,
- Quality,
- Black Belts,
- Training and Apprenticeship Instructors,
- Manufacturing Lead,
- Product Development,
- Sales and Marketing,
- Information Technology,
- Lead Analyst,
- Business Development,
- Continuous Improvement,
- Planning and Shipping,
- Designer,s and Design Engineers
- Information Security,
- Assembly,
- Legal and Corporate Affairs,
- Systems Development,
- President,
- CEO
- Owners
I am certain that I missed a few…
PMPA is proud to recognize our member and Vice President Darlene Miller, CEO of Permac Industries in Burnsville MN as one of this inaugural group of honorees.
“Darlene’s leadership reaches far beyond PERMAC. As a member of the President’s Council on Jobs and Competitiveness she recognized the need for trained high skill workers and led the creation of Right Skills Now training program and helped support the 10,000 Engineers nationwide engineering student retention program. She was named small business person of the year in 2008 by the U.S. Chamber, and serves as an officer and board member at PMPA as well as a number of other nonprofits.”
Congratulations to Darlene and all the women recognized for their vital role in manufacturing today. And thanks to the Manufacturing Institute for helping raise the awareness of the vital need for the talents that these and all women bring to our shops.
Yes, I would like to see my daughter get into manufacturing. Wouldn’t you?
“Manufacturing transforms more than materials into products. It transforms individuals into craftspeople. It transforms communities into global trade partners. It transforms companies into engines of human growth. It transforms our quality of life for the better.”- Darlene Miller
We were not surprised that the Manufacturing Institute recently selected PMPA member and 1st vice president Darlene Miller to be an inaugural STEP awards honoree.
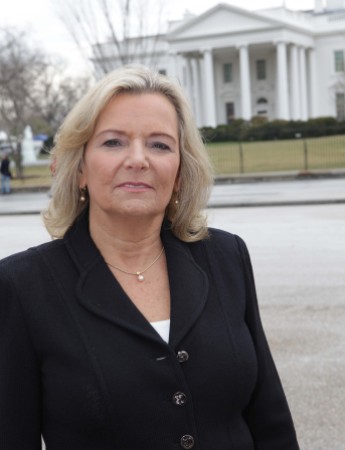
Manufacturing Institute: “…honored because they each made significant achievements in manufacturing through positive impact on their company and the industry as a whole.”
That’s a bit of an understatement.
Darlene’s leadership success reaches across the country and across organizations as she personally mentors at risk young women through Hope for Tomorrow, served as a member of the President’s Council for Jobs and Competitiveness (PCJC), and founded the Right Skills Now program to help meet the need for trained high skill workers in advanced manufacturing. She serves on a number of important committes for the U.S. Chamber Small Business Council, and is a frequent invitee, and presenter at various policy forums including the Clinton Global Initiative, The Atlantic Council and others. She promoted the nationwide adoption of the Right Skills Now training program and supported the creation of the 10,000 Engineers program, created to spur engineer retention by providing student internships. She advocates tirelessly for NIMS certifications and a credentialed workforce. She continues to work with additional schools across the company to make Right Skills Now readily available to potential machinists.
Darlene was named Small Business Person of the Year by The U.S. Chamber of Commerce in 2008, and the SBA in 2006 currently serves as Vice President of the Precision Machined Products Association, and was selected by her peers to be the association’s first female President in 2014.
We are proud to see our vice president and member Darlene Miller recognized for her efforts to promote manufacturing in North America. To promote manufacturing as a career. And to be recognized for her work at the national level to make a difference in the lives of talented but unemployed persons who are- thanks to her work with Right Skills Now- finding a career in advanced manufacturing.
PMPA extends our congratulations to Darlene Miller. And to the thousands of other individuals like her that are trying to make a difference in advancing our craft, our employees, and helping all find their highest and best use through careers in advanced manufacturing.
USA Today has an extensive article and video segment on Right Skills Now, the skilled workforce development program spearheaded by Darlene Miller of Permac Industries, in Burnsville, Minnesota.
Darlene is an elected vice president of PMPA and a member of the President’s Council on Jobs and Effectiveness (PCJC).

“We can’t wait two years or four years,” for students to graduate college, says Darlene Miller, CEO of Permac Industries, a contract manufacturer in Burnsville, Minn., who promoted the idea for the program last year when she was unable to find seven CNC operators. “We need people now.”
Experts say the program could serve as a national model for employers needing skilled workers yesterday and many jobless Americans unable to spend two years earning an associate degrees.
A pipeline of skilled factory workers is sorely needed, especially with Baby Boomers retiring. A year ago, 600,000 skilled manufacturing jobs were unfilled, and 80% of manufacturers couldn’t find proficient workers, according to a survey by the institute and Deloitte.
“Our programs, especially Rights Skills Now, are generated by industry needs.” Deborah Kerrigan, Dunwoody College of Technology. “There is a huge need for skilled labor.”
Read the full story and watch a great video at USA Today Right Skills Now
Darlene Miller was interviewed by President Bill Clinton at Clinton Global Initiative in Chicago recently.
Darlene Miller, President and CEO of Permac Industries, Vice President of PMPA, gave an employer’s perspective of Right Skills Now during a panel discussion about developing talent to continue economic recovery that has been led by manufacturing.
Darlene ‘s segment begins at 9:00 in the below video.
Clinton asks “Why is manufacturing recovering and growing again, and what are the constraints to finding workers, and what have you done about it?”
Miller answers “US manufactures as much as Brazil, Russia, India and China combined. We need skilled people- to fill over 600,000 openings we have. But we don’t need just labor, we need skilled people. We started Right Skills Now to help people get the skills they need for a career in Advanced Manufacturing.”
Video: Jumpstart America Clinton Global Initiative. (Advance to 9:00 to hear Mr. Clinton’s and Ms. Miller’s exchange.)
PMPA provides staff support to Ms. Miller and her work on the President’s Job Council and Right Skills Now. Our precision machining companies are looking for people with skills and talent to get a great career in advanced manufacturing.
High tech, get a well paying job, kind of skills.
Watch the video here.
PMPA Member Darlene Miller, member of the President’s Job Council and Creator/ Champion for RightSkillsNow said, “The skill set that we need, compared to ten years ago, is enormously different. Math skills, problem solving skills are absolutely critical.”
The students said they are excited and hopeful the skills they learn will lead them to a job and a lifetime of possibilities. Many local employers have stepped up to provide internships where the students can get additional time on task and real world experience.
Brandon Eide said, “It’s something to look forward to in the future, definitely.”